ECONOMIE
Nuits-Saint-Georges - Dans les coulisses de Constellium, spécialiste des produits en aluminium
Par Nadège Hubert
Publié le 21 Octobre 2023 à 07h58
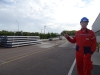
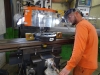
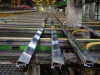
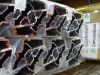
Difficile de quantifier le nombre d’objets du quotidien intégrant de l’aluminium qui sont passés dans la presse de Constellium à Nuits-Saint-Georges. Info-Beaune a poussé les portes des ateliers pour mieux appréhender le travail de cet industriel.
Dès le stationnement, en marche arrière sur le parking de Nuits-Saint-Georges, le visiteur comprend qu’il est sur un site industriel avec de nombreuses consignes de sécurité à respecter. Après une brève présentation de l’activité du groupe Constellium, spécialiste de la transformation de l’aluminium par extrusion qui compte 12 500 salariés dans le monde dont 35% en France, le directeur Jérôme Evrard met l’accent sur les règles à suivre pendant la visite du site de 16 000 mètres carrés couverts. « Ne touchez à rien car de l’aluminium chauffé à 500 degrés ne présente aucune différence avec de l’aluminium froid » précise-t-il notamment avant d’équiper le visiteur de l’indispensable tenue de sécurité : Lunettes de protection, bouchons d’oreille, chaussures de sécurité, blouse pour couvrir le corps, les bras et les jambes et l’indispensable casque pour prévenir de la chute d’objet. « Nous avons un code couleur pour les casques. Les bleus se destinent à nos 165 collaborateurs à l’exception des rouges qui concernent les sauveteurs secouristes et les verts pour les ambassadeurs environnement, les blancs sont réservés à la cinquantaine d’intérimaires, les oranges pour les sous-traitants et les jaunes pour les visiteurs. » Casque jaune sur la tête avec lunettes intégrées, chaussures de sécurité aux pieds, blouse orange et bleue immanquable… La visite peut commencer.
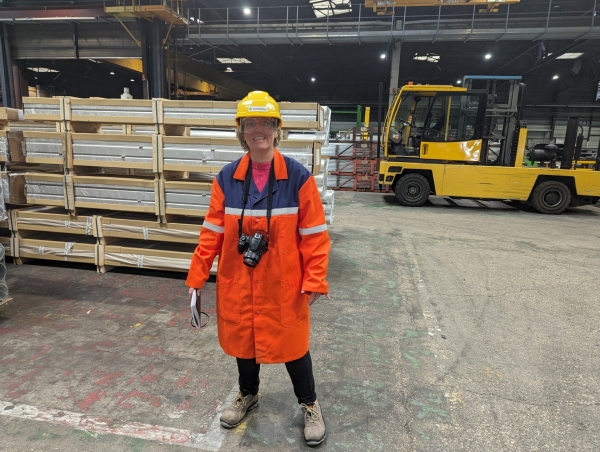
Une question de forme
Une fois quittés les bureaux de l’administration en passant par l’extérieur, impossible de ne pas remarquer les larges et longues billettes d’aluminium, des tubes pleins de matière prêts à l’utilisation. « Pour faire de l’extrusion, il faut la billette d’aluminium, un outil et une presse » résume le directeur de site. A partir d’un plan en deux dimensions, les équipes conçoivent l’outil nécessaire pour concevoir le produit attendu par les clients avant d’en confier la réalisation à un sous-traitant situé en France. « Il y a peu de limite à la créativité dans l’extrusion, nous pouvons imaginer toute sorte de formes pour les outils. » Une fois fabriqué par un partenaire, l’outil de retour sur le site de Constellium à Nuits-Saint-Georges, profitent des derniers réglages et ajustements réalisé par les techniciens pour pouvoir l’utiliser dans la presse située un peu plus loin dans le bâtiment. « Nous utilisons 2 500 formes par an. »
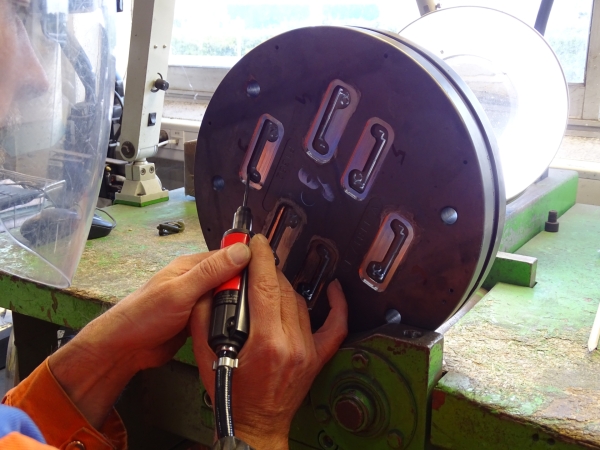
Constellium, ça presse !
Le directeur reprend la visite et s’arrête un instant devant l’atelier de maintenance voisin. « Nous avons un système informatique chargé de suivre la vie de chaque outil afin de savoir s’il doit repasser au réglage ou encore rejoindre le magasin. » La maintenance porte aussi sur les machines de l’atelier, les deux presses en particulier, mise à l’arrêt tous les 15 jours pour des opérations de maintenance prédictive. Derrière d’imposantes grilles de sécurité, l’une des deux est à l’œuvre dans un bruit assourdissant, justifiant les bouchons d’oreille. Avant de pénétrer dans la presse, le bloc d’aluminium est chauffé à 500 degrés. « L’un des enjeux de l’extrusion est d’avoir toujours la même température pour éviter les défauts de qualité. » Des capteurs et un process automatisé garantissent le contrôle de la donnée. Une fois chauffée, la billette rejoint automatiquement la presse qui lui donnera la forme attendue grâce aux outils conçus pour chaque client. L’aluminium entré sous forme cylindrique dans la presse ressort alors en profilé. « Entre temps, il a été refroidi à l’eau pour figer les caractéristiques techniques de l’aluminium. »
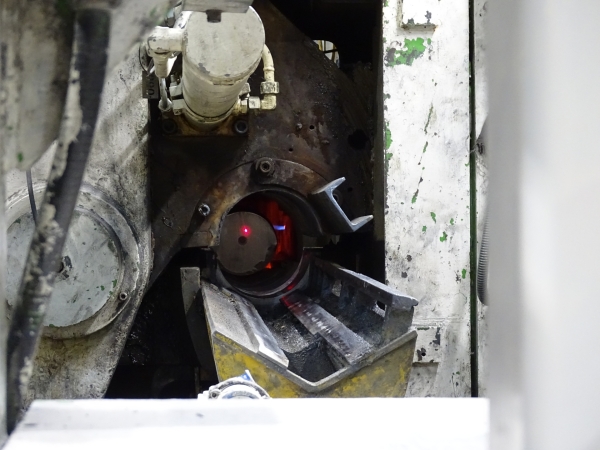
De long en large
Coupés à la longueur souhaitée, les profilés d’aluminium peuvent atteindre 50 mètres avant d’être tractionnés, autrement dit étirés, « pour enlever les contraintes métallurgiques de filage par extrusion. On ne peut pas tractionner à chaud donc on vérifie la température ». Le profilé passe une nouvelle fois à la coupe pour obtenir des morceaux de 13 mètres de long afin de tenir sur les véhicules de transport. « Les profilés rejoignent ensuite un four de traitement thermique. » En navigant entre les allées, les casques blancs croisent des casques bleus tandis que parfois un « Bonjour Jérôme » s’impose malgré le bruit des machines. Les salariés n’hésitent pas à appeler le directeur de site par son prénom. « Nous sommes dans une entreprise à taille humaine » sourit le premier concerné.
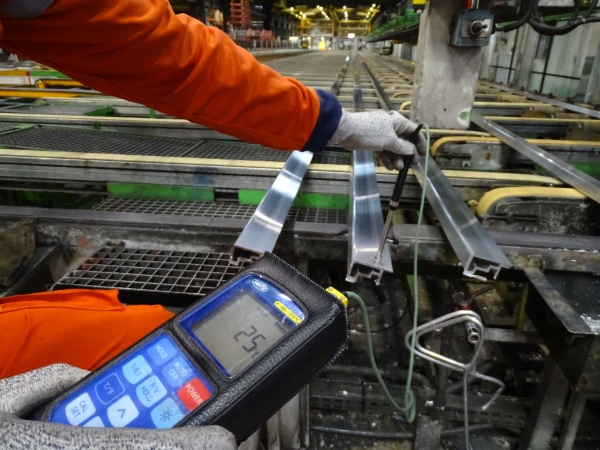
Découpe et qualité
Dans une allée, après avoir passé un feu vert pour les piétons afin d’éviter les engins de manutention, le responsable entre dans une cabine, le laboratoire qualité, où Sabrina réalise un contrôle de dureté du matériau jusqu’à la rupture. « Cela sert aussi à la traçabilité, tous les paramètres du process et de la presse sont suivis. » Une fois sectionné, l’élément rejoint un chariot comme il en existe plusieurs sur le site, pour envoyer l’aluminium au recyclage. « L’aluminium est recyclable à l’infini » insiste Jérôme Evrard. A côté, un autre laboratoire, dédié à la filière automobile, a pour mission de vérifier les pièces dans leur futur environnement, à l’équivalent de son futur emplacement dans le véhicule. En ressortant, le directeur atteint l’atelier de découpe complexe de profilé pour les plus petites pièces adjoint à un atelier qui poinçonne et grave certaines pièces d’aluminium.
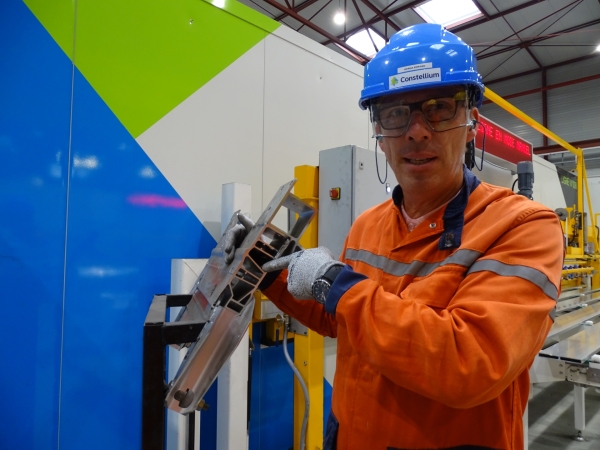
Du process au concret
Régulièrement au cours de la visite, l’œil tombe sur des vitrines pour valoriser les pièces conçues sur place et leur application mettant en avant la fierté du travail accompli. Une immense affiche de la Peugeot 3008 rappelle que Constellium Nuits-Saint-Georges conçoit les pare-chocs en aluminium du véhicule qui s’est vendu à 15 000 exemplaires par semaine depuis son lancement en 2016. En fin de process, l’atelier d’anodisation : « Il s’agit d’un traitement par électrolyse. Souvenez-vous de vos cours de classe de 4ème en physique, il faut créer un échauffement à la surface du profilé qui va transformer l’aluminium en oxyde d’aluminium. » Après une question sur le minerai le plus solide, le diamant, et le plus mou, le talc, le directeur précise que sur cette échelle, l’hydroxide d’aluminium se trouve juste après le diamant. « Nous allons générer une couche très dure et oxydée qui va protéger le profilé, notamment contre les intempéries. » Pour finir la visite, l’atelier d’emballage et de stockage non loin de là permet de prendre conscience de la diversité des applications de l’aluminium transformé par Constellium. « Ponton de marina, éolienne, voiture, enrouleur de bâche de piscine, poteaux de signalisation, élément de camion, métier à tisser, jante de vélo, connectique… » La visite s’achève au vestiaire pour rendre les équipements avant de rejoindre le parking grâce au directeur qui aura ouvert les contrôles d’accès indispensables pour sortir. Si le site est sécurisé, il reste ouvert au candidat désireux d’intégrer le groupe !
Nadège Hubert
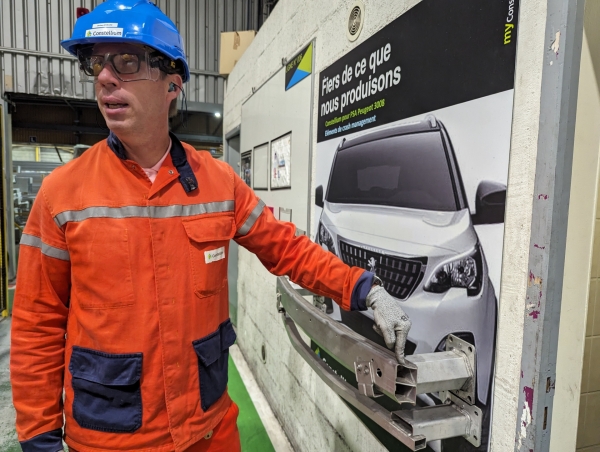
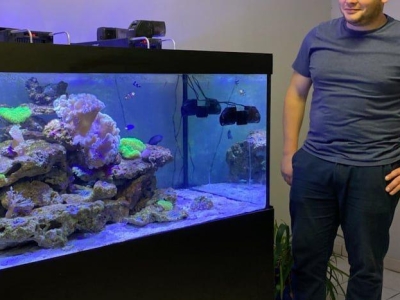
-
Meursault - Sur les traces de « La Grande Vadrouille » : une visite guidée inoubliable
-
Beaune - Le nouveau stade nautique se dévoile
-
Beaune - Manon Chaussin, l'élégance bourguignonne en lice pour Miss Élégance France 2024
-
Beaune - The American Bar, le sanctuaire de l'art des cocktails, spiritueux et vins d'exception
-
Bligny-sur-Ouche - Les Red Amazones, deux pompiers volontaires engagées pour une noble cause
-
Beaune – Le timing des travaux place Madeleine est respecté
-
Beaune - Le skateboard revisité : quand l'art antique s'invite au Musée des Beaux-Arts avec Romain Hurdequint
-
Les Rencontres Régionales de Cirque à Beaune - Trois jours d'émerveillement et de partage pour une centaine de circassiens
-
Le retour de la consigne sur le verre à Beaune
-
Chaudenay - « Chez Armand », une parenthèse gourmande et authentique
-
Concours Miss Élégance France 2024 - Manon Chaussin, Miss Élégance Bourgogne 2023, frôle la demi-finale
-
Beaune - 3e édition du Salon Prestige Auto du 3 au 5 mai : un rendez-vous luxueux
-
Météo en Côte-d’Or – Une semaine entre soleil et averses
-
Météo en Côte-d’Or – Week-end pluvieux en perspective
-
Campagne européenne - Besoin d'Europe 71 mobilise les citoyens sur le marché de Chagny
-
Beaune - 21e bourse de véhicules anciens avec Les Chevronnés à Vignoles le dimanche 28 avril
-
Beaune - Les Concerts de Printemps de Jazz O' Verre : une symphonie enivrante de jazz et de saveurs les 27 et 30 avril
-
« Bienvenue à Savigny » - Découvrez les trésors de Savigny lors de son festival viticole annuel les 4 et 5 mai
-
La Communauté d'Agglomération Beaune Côte & Sud lance une enquête sur les logements vacants
-
Beaune – 2e édition du Tremplin Émergences : appel aux talents musicaux locaux
-
Beaune – Les immanquables de ce mois de mai à l’Hôtel-Dieu
-
16e édition du Festival Musique & Vin au Clos Vougeot - Une symphonie d'émotions et de saveurs du 22 au 30 juin